Maintenance technicians will need to do some preparation for their next interview. This post includes 50 interview questions for maintenance technicians to help them know the ins and outs of the standard interview process for their field.
Preparing for a maintenance technician interview?
Sign up for Huntr to help you access mock interview questions, follow-up email templates, and get feedback on your resume.
How to Prepare for a Maintenance Technician Interview
1. Review Technical Skills and Certifications
Make sure you are familiar with the technical skills and certifications relevant to the job. Review the specific tools, equipment, and software you will be expected to use. Be prepared to discuss your experience with troubleshooting, repairing, and maintaining various systems such as HVAC, electrical, plumbing, and machinery. Highlight any relevant certifications you hold, such as EPA certification for refrigerant handling or a journeyman electrician license.
2. Prepare to Discuss Problem-Solving and Troubleshooting
Maintenance Technician roles require strong problem-solving skills. Be ready to provide examples of how you have diagnosed and resolved complex maintenance issues in the past. Explain your approach to troubleshooting problems, including how you identify the root cause, determine the best course of action, and implement effective solutions. Highlight your ability to work under pressure and manage unexpected breakdowns efficiently.
3. Emphasize Safety and Preventative Maintenance
Safety is a critical aspect of maintenance work. Be prepared to discuss your knowledge of safety protocols, OSHA regulations, and how you ensure a safe working environment. Explain your experience with preventative maintenance programs, including how you schedule and perform routine inspections and maintenance tasks to prevent equipment failures and extend the lifespan of machinery. Provide examples of how you have contributed to a culture of safety in your previous roles.
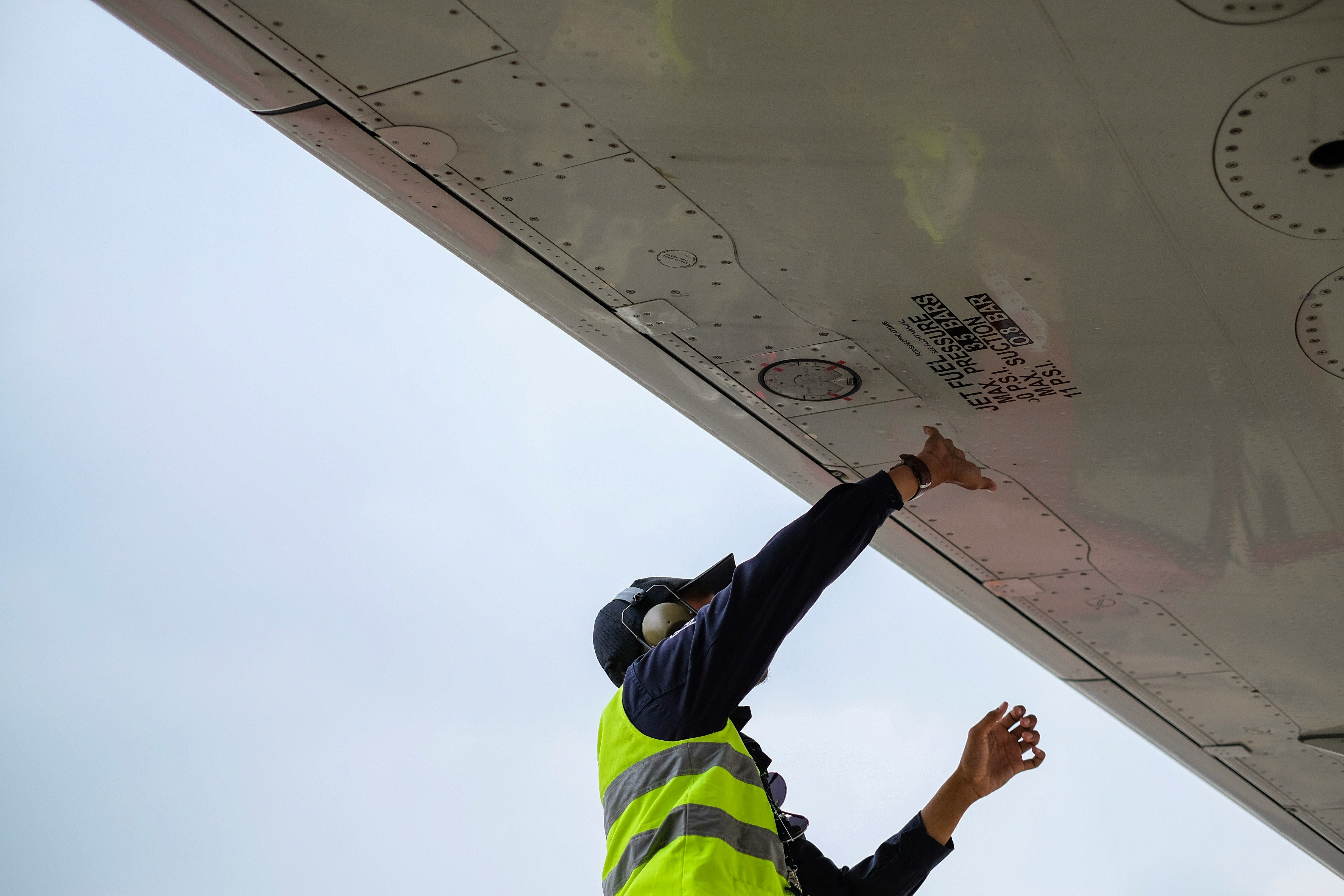
Maintenance Technician Skills to Highlight in Your Interview
1. Technical Proficiency and Hands-On Experience
Emphasize your technical skills and hands-on experience with various systems such as HVAC, electrical, plumbing, and mechanical. Discuss your familiarity with diagnostic tools, maintenance software, and your ability to read and interpret blueprints and technical manuals.
2. Problem-Solving and Troubleshooting
Highlight your strong problem-solving abilities and experience in troubleshooting complex maintenance issues. Provide examples of how you have identified root causes, developed solutions, and successfully resolved equipment failures or system malfunctions.
3. Preventative Maintenance
Showcase your experience with preventative maintenance programs. Explain how you have conducted routine inspections, performed regular maintenance tasks, and implemented strategies to prevent equipment failures. Highlight your ability to plan and prioritize maintenance activities to ensure operational efficiency.
4. Safety Awareness and Compliance
Discuss your commitment to safety and compliance with industry regulations and standards. Provide examples of how you have followed safety protocols, adhered to OSHA regulations, and promoted a safe working environment. Emphasize your training in safety procedures and your proactive approach to identifying and mitigating potential hazards.
5. Communication and Teamwork
Highlight your strong communication and teamwork skills. Explain how you have effectively communicated with supervisors, colleagues, and other departments to coordinate maintenance activities and resolve issues. Provide examples of how you have collaborated with team members to achieve maintenance goals and improve overall efficiency.
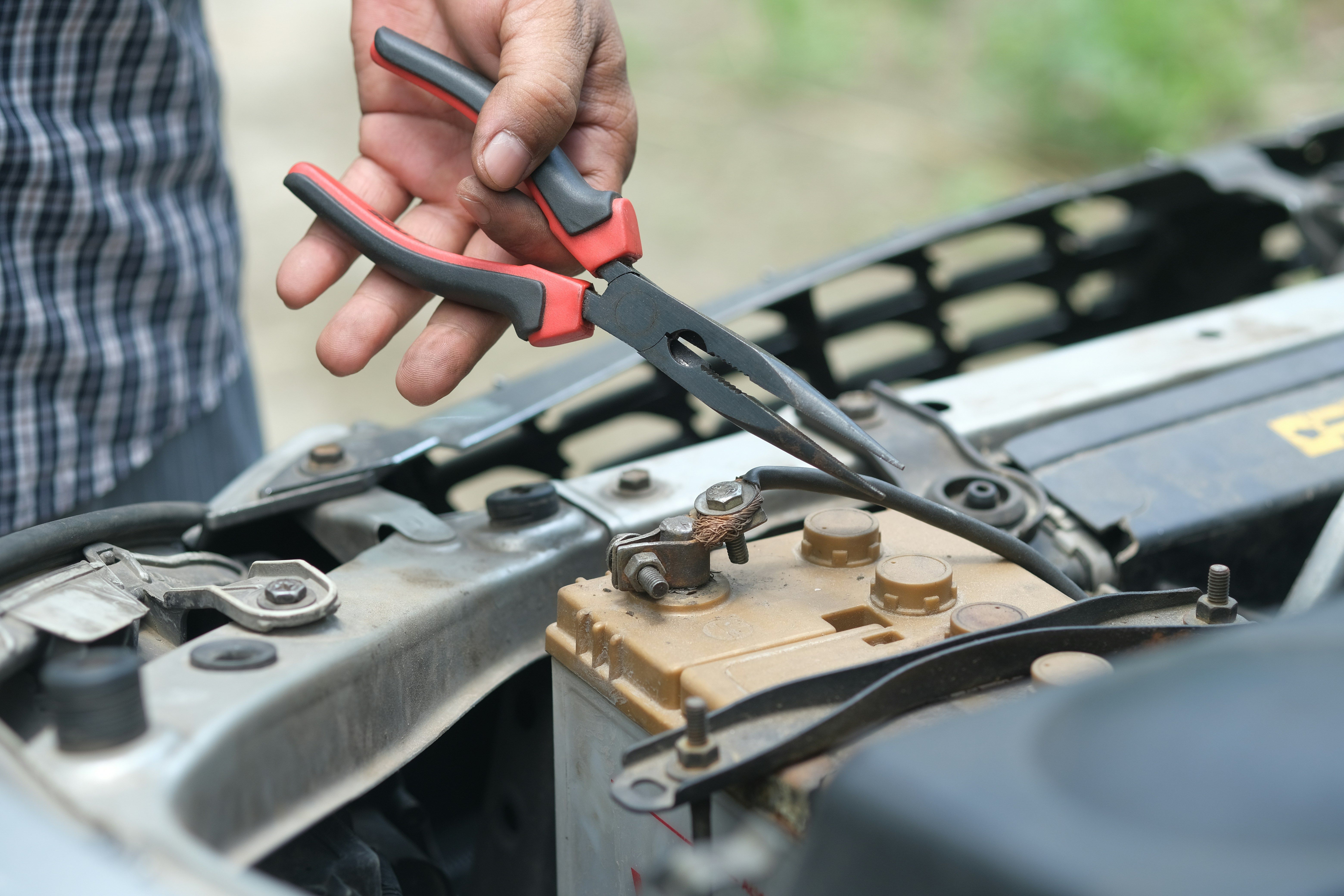
50 Interview Questions For Maintenance Technician
1. Can you describe your previous experience as a Maintenance Technician?
In my previous role as a Maintenance Technician, I was responsible for maintaining and repairing various types of equipment and systems in a large manufacturing facility. My duties included troubleshooting mechanical, electrical, and HVAC systems, performing preventative maintenance, and responding to emergency repair requests. I collaborated closely with other departments to ensure minimal disruption to operations and maintained detailed records of all maintenance activities.
2. What types of systems and equipment have you worked with?
I have worked with a wide range of systems and equipment, including HVAC systems, electrical circuits, plumbing systems, mechanical machinery, and building automation systems. My experience also includes working with refrigeration units, fire safety systems, and various types of industrial equipment used in manufacturing processes.
3. How do you prioritize your tasks when handling multiple maintenance requests?
I prioritize tasks based on the urgency and impact on operations. I assess the severity of the issue, the potential risk to safety, and the effect on production or building functionality. By communicating with supervisors and using a maintenance management system to track and schedule tasks, I ensure that the most critical issues are addressed first while also managing routine maintenance efficiently.
4. Can you give an example of a time when you successfully diagnosed and repaired a complex issue?
I once faced a situation where a critical piece of machinery was repeatedly failing, causing significant downtime. After a thorough inspection and analysis, I identified that the issue was due to a faulty sensor that was intermittently sending incorrect signals. I replaced the sensor, recalibrated the system, and implemented a monitoring protocol to prevent future occurrences. This repair not only resolved the immediate issue but also improved the overall reliability of the machinery.
5. How do you stay updated with the latest maintenance techniques and technologies?
I stay updated by regularly attending industry workshops, training sessions, and certification courses. I also read technical manuals, industry publications, and online forums to learn about new tools and technologies. Networking with other professionals in the field and participating in professional organizations also helps me stay informed about the latest trends and best practices in maintenance.
6. Describe your experience with preventative maintenance programs.
I have extensive experience developing and implementing preventative maintenance programs. This involves scheduling regular inspections and servicing of equipment to prevent unexpected failures. I use maintenance management software to track maintenance activities, analyze equipment performance data, and adjust schedules as needed. By conducting regular maintenance, we can extend the lifespan of equipment and reduce downtime.
7. How do you ensure that you are following safety protocols and regulations?
I ensure compliance with safety protocols and regulations by thoroughly understanding the relevant guidelines and incorporating them into my daily work practices. I attend regular safety training sessions and stay informed about updates to safety regulations. I also conduct safety audits, use proper personal protective equipment (PPE), and follow established procedures to minimize risks.
8. Can you explain how you troubleshoot electrical systems?
When troubleshooting electrical systems, I start by reviewing the system's schematic diagrams and identifying potential problem areas. I use tools like multimeters and circuit testers to diagnose issues such as faulty wiring, short circuits, or malfunctioning components. By systematically isolating and testing each part of the system, I can accurately identify and repair the problem.
9. What is your approach to handling emergency repairs?
In emergency repair situations, I prioritize quick and effective responses to minimize downtime and ensure safety. I assess the situation, gather necessary tools and parts, and communicate with relevant personnel about the issue and expected resolution time. I work efficiently to diagnose and fix the problem while ensuring that all safety protocols are followed.
10. How do you document your maintenance work?
I document my maintenance work by recording detailed notes on the nature of the problem, the steps taken to resolve it, and any parts used. I use maintenance management software to enter this information, ensuring that records are accurate and up-to-date. This documentation helps track the history of equipment maintenance and informs future repair and maintenance decisions.
11. Can you give an example of a time when you improved a maintenance process?
I identified that our HVAC system's filter replacement schedule was not optimal, leading to frequent airflow issues. I conducted a study to determine the ideal replacement frequency and implemented a new schedule. This change reduced system strain, improved air quality, and lowered maintenance costs by preventing unnecessary replacements and system breakdowns.
12. Describe your experience with HVAC systems.
I have extensive experience with HVAC systems, including installation, maintenance, and repair. I have worked on both residential and commercial systems, performing tasks such as inspecting and replacing filters, cleaning ducts, checking refrigerant levels, and troubleshooting electrical and mechanical components. My goal is to ensure that HVAC systems operate efficiently and reliably.
13. How do you handle pressure when there are urgent maintenance issues to resolve?
I handle pressure by staying calm and focused, prioritizing tasks based on their urgency and impact. I rely on my training and experience to quickly assess the situation and develop an action plan. Effective communication with my team and supervisors is crucial to ensure that everyone is informed and aligned. By maintaining a methodical approach, I can resolve urgent issues efficiently and effectively.
14. What steps do you take to ensure the longevity of the equipment you maintain?
To ensure equipment longevity, I follow a comprehensive preventative maintenance program that includes regular inspections, cleaning, lubrication, and timely replacement of worn parts. I also monitor equipment performance data to identify potential issues early and address them before they lead to major failures. Using high-quality parts and adhering to manufacturer guidelines further contributes to extending the life of the equipment.
15. Can you explain how you would handle a situation where a piece of equipment keeps failing repeatedly?
If a piece of equipment keeps failing, I would conduct a thorough root cause analysis to identify the underlying issue. This may involve reviewing maintenance records, inspecting the equipment, and consulting with colleagues or manufacturers. Once the root cause is identified, I would implement a targeted solution, such as replacing a faulty component, updating maintenance procedures, or providing additional training to operators. Monitoring the equipment's performance after the repair ensures that the issue has been resolved.
16. How do you ensure effective communication with your team and supervisors?
I ensure effective communication by maintaining open and regular communication channels with my team and supervisors. I provide updates on maintenance activities, share important information, and seek feedback. Regular team meetings and use of communication tools like emails, messaging apps, and maintenance management software help keep everyone informed and aligned.
17. Describe your experience with plumbing systems.
I have experience with various plumbing systems, including installation, maintenance, and repair of pipes, fixtures, and appliances. I have worked on tasks such as fixing leaks, clearing blockages, installing new plumbing systems, and maintaining water heaters. My goal is to ensure that plumbing systems operate efficiently and safely.
18. How do you manage your time when dealing with multiple work orders?
I manage my time by prioritizing work orders based on their urgency and importance. I use maintenance management software to schedule and track tasks, ensuring that I stay organized and meet deadlines. Effective time management involves balancing routine maintenance with urgent repairs and communicating with supervisors to adjust priorities as needed.
19. Can you provide an example of a time when you had to work with minimal supervision?
In a previous role, I was tasked with completing a complex electrical repair while my supervisor was unavailable. I relied on my training and experience to diagnose and repair the issue independently. I documented my work thoroughly and provided a detailed report to my supervisor upon completion. Successfully handling this task demonstrated my ability to work autonomously and maintain high standards.
20. What tools and software are you proficient in using for maintenance tasks?
I am proficient in using a variety of tools and software for maintenance tasks, including multimeters, wrenches, pliers, screwdrivers, and power tools. I also use maintenance management software like CMMS (Computerized Maintenance Management Systems) to track work orders, schedule maintenance, and document repairs. Familiarity with diagnostic tools and equipment-specific software helps me efficiently troubleshoot and maintain various systems.
21. How do you approach training and mentoring new maintenance staff?
I approach training and mentoring new maintenance staff by providing hands-on guidance and sharing my knowledge and experience. I start with an overview of safety protocols and basic maintenance procedures, gradually introducing more complex tasks. I encourage questions, provide constructive feedback, and involve new staff in real-world scenarios to help them build confidence and skills. Regular check-ins and ongoing support ensure that they continue to develop and succeed in their roles.
22. Can you describe a situation where you had to work with other departments to resolve a maintenance issue?
I worked with the production and quality control departments to resolve an issue with a critical piece of machinery that was affecting product quality. By collaborating closely with these departments, we identified the root cause of the problem—a misaligned component—and implemented a solution. This teamwork ensured that the machinery was repaired quickly and production could resume without further issues.
23. How do you stay organized and keep track of your maintenance tasks and schedules?
I stay organized by using maintenance management software to schedule and track tasks. I create detailed records of maintenance activities, set reminders for routine tasks, and prioritize work orders based on urgency and impact. Regularly reviewing my schedule and adjusting as needed helps ensure that I stay on top of my responsibilities and meet deadlines.
24. Describe your experience with mechanical systems.
I have extensive experience with mechanical systems, including motors, pumps, conveyors, and other industrial machinery. My work involves routine inspections, lubrication, alignment, and troubleshooting mechanical failures. I use diagnostic tools and techniques to identify issues and perform repairs to ensure that mechanical systems operate efficiently and reliably.
25. How do you handle situations where you don’t have all the information or resources you need to complete a repair?
When faced with incomplete information or resources, I first try to gather as much relevant information as possible by consulting manuals, schematics, and colleagues. I communicate with supervisors to request additional resources or support if needed. If immediate resolution is not possible, I document the issue and develop a temporary solution to minimize impact until the necessary information or resources are available.
26. Can you give an example of how you have contributed to a culture of safety in the workplace?
I contributed to a culture of safety by leading safety training sessions and promoting the use of proper personal protective equipment (PPE). I also conducted regular safety audits to identify and address potential hazards. By encouraging open communication about safety concerns and recognizing team members who followed safety protocols, I helped foster a workplace environment where safety was a top priority.
27. How do you handle feedback and criticism about your maintenance work?
I handle feedback and criticism by listening actively and maintaining a positive attitude. I view feedback as an opportunity for growth and improvement. I reflect on the feedback, identify areas for improvement, and take actionable steps to enhance my skills and performance. By being open to constructive criticism, I can continually improve the quality of my work.
28. What is your experience with energy management and efficiency improvements?
I have experience implementing energy management and efficiency improvements, such as optimizing HVAC systems, upgrading lighting to energy-efficient alternatives, and improving insulation. I also conduct energy audits to identify areas for improvement and develop action plans to reduce energy consumption. These initiatives help lower operating costs and contribute to a more sustainable facility.
29. How do you ensure that maintenance activities cause minimal disruption to operations?
I ensure minimal disruption by planning maintenance activities during off-peak hours or scheduled downtime. I communicate with relevant departments to coordinate timing and provide advance notice of any potential disruptions. By efficiently executing maintenance tasks and having contingency plans in place, I minimize the impact on operations and maintain productivity.
30. Describe a time when you had to learn a new skill or technology quickly to complete a job.
I was once assigned to repair a newly installed automated control system that I was not familiar with. I quickly reviewed the system's manuals, attended a brief training session, and consulted with the manufacturer’s technical support. By rapidly acquiring the necessary knowledge and applying it, I was able to diagnose and repair the system, ensuring minimal downtime.
31. How do you assess whether to repair or replace a piece of equipment?
I assess whether to repair or replace equipment by evaluating the cost of repairs, the equipment's age, and its overall condition. I also consider the frequency of breakdowns and the impact on operations. If the repair costs are high or the equipment is nearing the end of its useful life, replacement may be more cost-effective. I consult with supervisors and use data to support my recommendations.
32. Can you provide an example of a time when you had to manage a significant maintenance project?
I managed a project to upgrade the HVAC system in our facility. This involved coordinating with contractors, scheduling the work to minimize disruption, and ensuring compliance with safety and building codes. I oversaw the installation, conducted inspections, and managed the budget. The successful completion of the project resulted in improved system efficiency and reduced energy costs.
33. How do you handle conflicts or disagreements with colleagues or supervisors?
I handle conflicts by addressing issues directly and professionally. I listen to the other party's perspective, express my own views respectfully, and seek common ground. If necessary, I involve a neutral third party to mediate the discussion. By maintaining open communication and focusing on solutions, I can resolve conflicts constructively and maintain positive working relationships.
34. Describe your experience with building automation systems.
I have experience with building automation systems, including installation, programming, and maintenance. I work with systems that control HVAC, lighting, security, and other building functions. My tasks include configuring settings, troubleshooting issues, and ensuring that the systems operate efficiently. By optimizing these systems, I can enhance building performance and reduce energy consumption.
35. What is your approach to preventive maintenance scheduling?
My approach to preventive maintenance scheduling involves using maintenance management software to create and track schedules for regular inspections and servicing of equipment. I consider manufacturer recommendations, equipment usage patterns, and historical data to determine the optimal frequency for maintenance tasks. Regularly reviewing and adjusting the schedule ensures that we address potential issues before they lead to major failures.
36. How do you ensure that you maintain high standards of quality in your work?
I maintain high standards of quality by following best practices and manufacturer guidelines for maintenance tasks. I use high-quality parts and tools, conduct thorough inspections, and test equipment after repairs to ensure proper functionality. Continuous learning and staying updated with industry standards also help me maintain high-quality work.
37. Can you give an example of a time when you had to work under tight deadlines?
I was once tasked with repairing a critical piece of machinery that broke down just before a major production run. I quickly diagnosed the issue, sourced the necessary parts, and completed the repair within a few hours. By working efficiently and staying focused under pressure, I ensured that the production schedule was maintained and downtime was minimized.
38. How do you handle situations where you have to make quick decisions without consulting your supervisor?
In situations requiring quick decisions, I rely on my training and experience to assess the situation and determine the best course of action. I prioritize safety and consider the potential impact on operations. I document my decision and actions taken and inform my supervisor as soon as possible. By staying calm and using my judgment, I can make effective decisions in urgent situations.
39. Describe your experience with fire safety systems.
I have experience with fire safety systems, including installation, maintenance, and testing of fire alarms, sprinkler systems, and fire extinguishers. I conduct regular inspections and tests to ensure that all components are functioning correctly and comply with safety regulations. I also provide training to staff on fire safety procedures and ensure that all documentation is up-to-date.
40. How do you ensure that you comply with environmental regulations in your maintenance work?
I ensure compliance with environmental regulations by staying informed about relevant laws and guidelines. I follow proper procedures for handling hazardous materials, disposing of waste, and using energy-efficient practices. Regular training and audits help ensure that my work meets environmental standards and contributes to a sustainable workplace.
41. Can you provide an example of a time when you improved the efficiency of a maintenance operation?
I improved the efficiency of our maintenance operation by implementing a new maintenance management software system. This system streamlined work order tracking, scheduling, and inventory management. As a result, we reduced response times for repair requests, improved communication within the team, and optimized our inventory levels, leading to cost savings and increased productivity.
42. How do you handle routine maintenance tasks versus emergency repairs?
I balance routine maintenance tasks and emergency repairs by prioritizing based on urgency and impact. Routine tasks are scheduled during regular hours, while emergency repairs are addressed immediately to minimize downtime. I use maintenance management software to track and adjust schedules as needed, ensuring that both types of tasks are managed effectively.
43. Describe your experience with inventory management for maintenance supplies.
I have experience managing inventory for maintenance supplies, including tracking stock levels, ordering parts, and managing suppliers. I use inventory management software to maintain accurate records and ensure that we have the necessary parts on hand for routine maintenance and emergency repairs. Regular audits help identify any discrepancies and optimize inventory levels.
44. How do you stay motivated and maintain a positive attitude during challenging maintenance tasks?
I stay motivated by focusing on the satisfaction of resolving issues and improving equipment performance. I set clear goals for each task and break them down into manageable steps. Positive reinforcement from colleagues and supervisors also helps maintain motivation. By staying organized and maintaining a problem-solving mindset, I can overcome challenges and stay positive.
45. Can you explain how you troubleshoot and repair refrigeration systems?
When troubleshooting refrigeration systems, I start by checking the most common issues, such as refrigerant levels, thermostat settings, and electrical connections. I use diagnostic tools to measure pressure and temperature, identify leaks, and test components like compressors and evaporators. Once the issue is diagnosed, I perform the necessary repairs, replace faulty parts, and test the system to ensure proper operation.
46. How do you ensure that maintenance records are accurate and up-to-date?
I ensure that maintenance records are accurate and up-to-date by documenting all activities immediately after completing a task. I use maintenance management software to enter details about the problem, the steps taken to resolve it, and any parts used. Regular audits of the records help identify and correct any discrepancies, ensuring that we have a complete and accurate maintenance history.
47. Describe a time when you had to work in a team to complete a large maintenance project.
I worked on a team project to upgrade the electrical system in our facility. This involved coordinating with electricians, engineers, and other maintenance staff. We developed a detailed project plan, assigned specific tasks, and held regular progress meetings. Effective communication and collaboration ensured that the project was completed on time and within budget, with minimal disruption to operations.
48. How do you handle working in hazardous or uncomfortable conditions?
I handle working in hazardous or uncomfortable conditions by following safety protocols and using the appropriate personal protective equipment (PPE). I assess the risks and take necessary precautions to ensure my safety and that of my colleagues. Staying focused, maintaining a positive attitude, and being prepared for challenging environments help me perform effectively in such conditions.
49. Can you give an example of a time when you had to adapt to a major change in your maintenance procedures?
Our facility underwent a major upgrade to a new maintenance management software system. I had to adapt to new procedures for tracking work orders, scheduling tasks, and managing inventory. I attended training sessions and practiced using the new system to become proficient. This change improved our overall efficiency and streamlined our maintenance processes.
50. How do you prioritize safety in your daily maintenance activities?
I prioritize safety by following established protocols, using proper PPE, and conducting thorough risk assessments before starting any task. I stay informed about safety regulations and attend regular training sessions. By maintaining a safety-first mindset and encouraging my team to do the same, I ensure that we minimize risks and create a safe working environment.