As companies work towards becoming more efficient, employees are tasked with improving processes in their workflow to produce more results, faster. Not only do companies see improved quality but they also ship more efficiently. This post has 50 interview questions about process improvement and more.
Faster job search. More Offers.
Use our AI Cover Letter Builder, Interview Prep and Job Search Tools to land your next job.
What is process improvement?
Process improvement is a strategic approach aimed at enhancing the efficiency and effectiveness of an organization's operations. It involves critically examining current processes to identify bottlenecks, redundancies, or inefficiencies and then implementing targeted strategies to streamline workflows, reduce waste, and increase productivity. By focusing on continual improvement, organizations can adapt more quickly to market changes, improve customer satisfaction, and achieve better overall performance. This soft skill not only requires analytical capabilities to dissect and understand complex processes but also demands creativity and problem-solving skills to devise and implement innovative solutions.
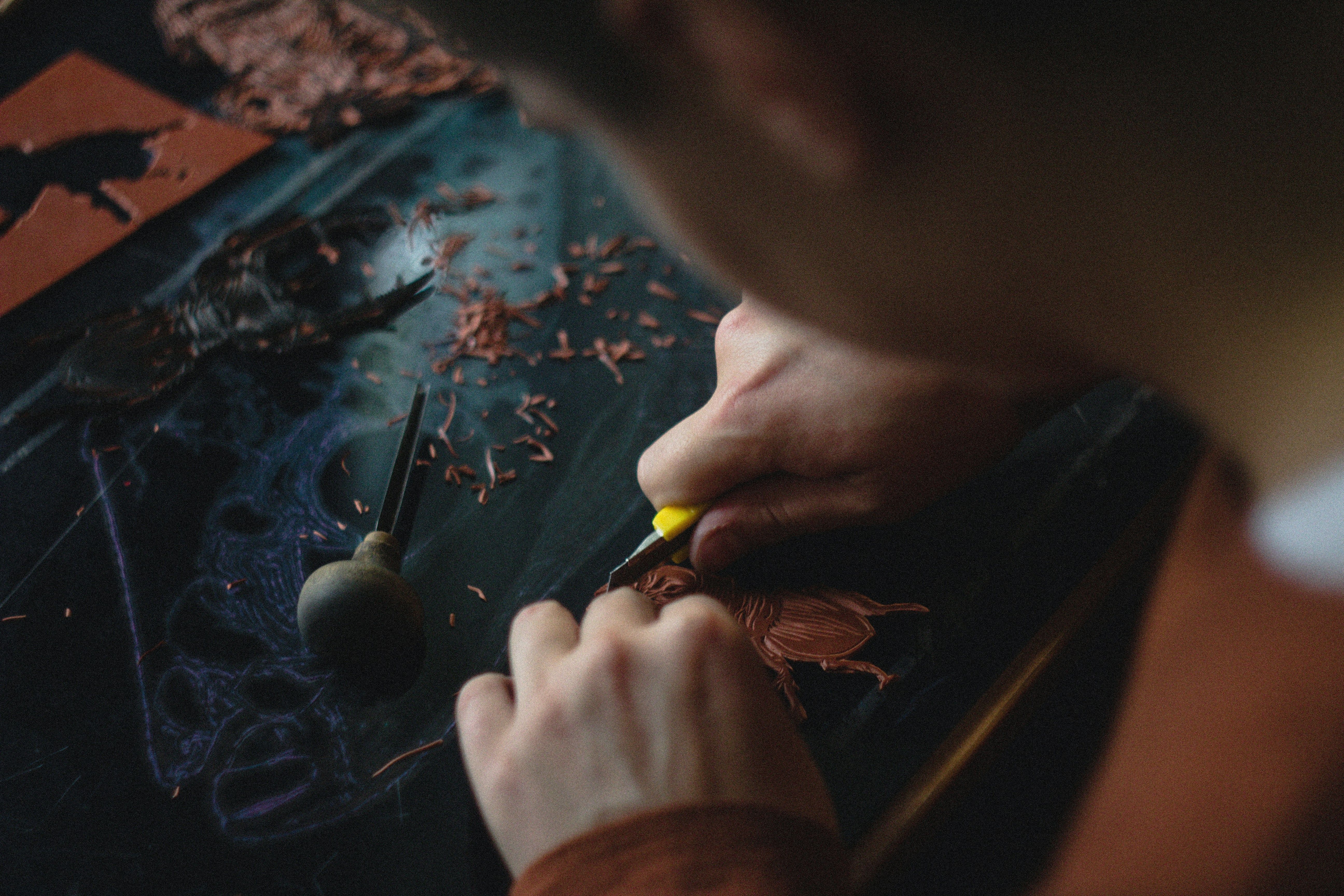
Why is process improvement important in the workplace?
1. Boosts Efficiency
Mastering the skill of process improvement is crucial in the workplace as it directly contributes to enhancing operational efficiency. By identifying bottlenecks, streamlining workflows, and optimizing resources, employees can significantly reduce time and costs associated with various tasks. This not only speeds up production rates but also allows teams to allocate their efforts more effectively, leading to increased productivity across the board.
2. Enhances Quality
Process improvement plays a pivotal role in elevating the quality of output. By continuously evaluating and refining processes, employees can minimize errors and inconsistencies, ensuring that the final product or service meets or exceeds the desired standards. This relentless pursuit of excellence is key to maintaining a competitive edge in the market, satisfying customer expectations, and fostering a culture of quality within the organization.
3. Promotes Innovation
At its core, process improvement is about challenging the status quo and seeking better ways of doing things. This skill encourages employees to think critically and creatively, leading to innovative solutions that can revolutionize how work is done. By fostering an environment where innovation is embraced, companies can adapt more swiftly to changing market dynamics, explore new opportunities, and remain at the forefront of their industry.
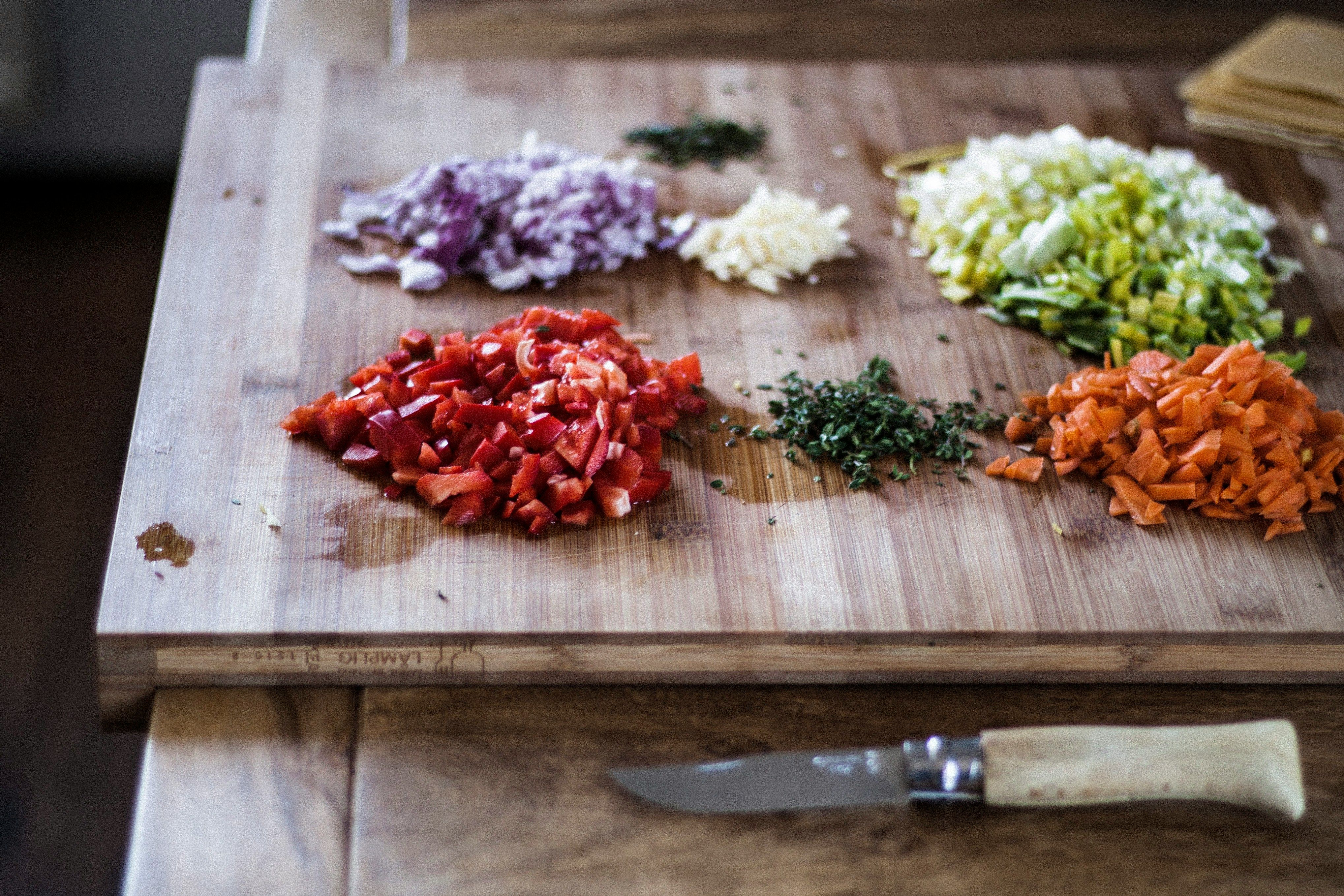
Five Tips for Answering Process Improvement Interview Questions
1. Understand the Core of Process Improvement
Before stepping into the interview, ensure you have a solid understanding of what process improvement entails. It's not just about making things faster or cheaper; it's about optimizing workflows to increase efficiency, reduce waste, and enhance quality. Familiarize yourself with methodologies like Lean, Six Sigma, and Kaizen, as these are often referenced in discussions around process improvement.
2. Use the STAR Method
When answering process improvement questions, structure your responses using the STAR method (Situation, Task, Action, Result). This technique will help you provide a clear and concise answer. For instance, describe a specific Situation where you identified a process that needed improvement, outline the Task or goal, detail the Actions you took to improve the process, and highlight the Results achieved.
3. Highlight Your Analytical Skills
Process improvement is deeply analytical. Employers want to know you can dissect a process, identify inefficiencies, and propose actionable solutions. When answering questions, emphasize your ability to use data analysis tools, conduct root cause analyses, and apply critical thinking to solve complex problems.
4. Showcase Soft Skills
While the technical aspects of process improvement are crucial, don't overlook the importance of soft skills. Change often meets resistance, so highlight your ability to communicate effectively, manage stakeholder expectations, and lead a team through a transition period. Provide examples of how you've navigated these challenges in past roles.
5. Reflect on Continuous Improvement
Finally, demonstrate your commitment to continuous improvement, not just as a one-time project but as an ongoing mindset. Discuss how you stay updated with the latest process improvement trends and technologies. Share how you've fostered a culture of improvement within your teams, encouraging feedback and innovation to continually enhance workflows.
By preparing with these tips, you'll be well-equipped to answer process improvement interview questions, showcasing your expertise and how you can bring value to the organization.
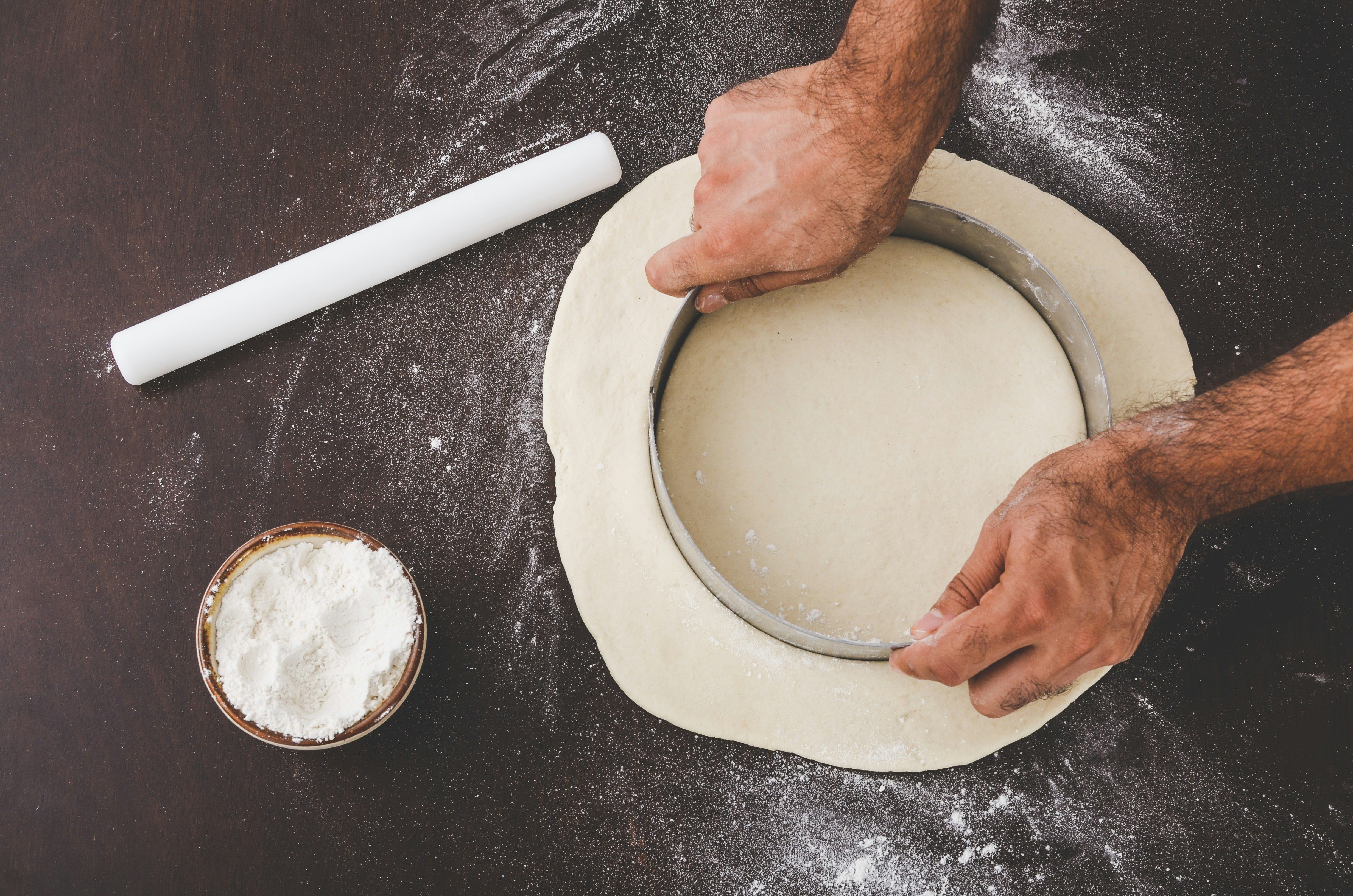
50 Interview Questions About Process Improvement (With Answers)
1. Can you describe a time when you identified a need for process improvement in your previous role?
In my previous role, I identified a need for process improvement in our inventory management system. We frequently encountered stock discrepancies, leading to delayed shipments and customer dissatisfaction. By conducting a thorough analysis, I discovered that manual data entry errors were the primary cause. This led to the implementation of an automated inventory tracking system, which significantly reduced errors and improved overall efficiency.
2. How do you prioritize which processes need improvement within an organization?
I prioritize processes needing improvement by assessing their impact on overall business performance, customer satisfaction, and operational efficiency. Critical processes that directly affect customer experience or contribute significantly to cost and time inefficiencies are addressed first. Regular feedback from team members and stakeholders also helps identify high-priority areas.
3. What steps do you take to analyze a process before making recommendations for improvement?
To analyze a process, I first map out the current workflow to understand each step involved. I then gather data through observations, interviews, and performance metrics. Identifying bottlenecks, redundancies, and pain points is crucial. Finally, I benchmark against industry best practices and use root cause analysis to determine underlying issues before making recommendations.
4. Can you share an example of a successful process improvement initiative you led or participated in?
I led a process improvement initiative to streamline our customer onboarding process. By integrating a CRM system and automating repetitive tasks, we reduced the onboarding time from two weeks to three days. This improvement enhanced customer satisfaction, increased conversion rates, and allowed the sales team to focus more on building relationships rather than administrative tasks.
5. How do you measure the success of a process improvement project?
Success is measured by comparing key performance indicators (KPIs) before and after implementation. Metrics such as time savings, cost reduction, error rates, and customer satisfaction levels are crucial. Regular feedback from stakeholders and continuous monitoring ensure the improvements are effective and sustained over time.
6. What tools or methodologies do you use when working on process improvement?
I use methodologies such as Lean, Six Sigma, and PDCA (Plan-Do-Check-Act). Tools like process mapping software, flowcharts, and data analysis tools (e.g., Excel, Tableau) help visualize and analyze processes. Additionally, root cause analysis techniques like the 5 Whys and fishbone diagrams are essential in identifying underlying issues.
7. How do you involve team members or stakeholders in the process improvement planning?
I involve team members and stakeholders through collaborative workshops, brainstorming sessions, and regular meetings. Their input is invaluable as they are directly involved in the processes. By fostering an inclusive environment, I ensure that their insights and concerns are considered, leading to more effective and accepted improvements.
8. Can you explain how process improvement can impact customer satisfaction?
Process improvement enhances customer satisfaction by reducing errors, improving response times, and increasing service reliability. Streamlined processes lead to quicker, more accurate deliveries and better overall customer experiences. Satisfied customers are more likely to return and recommend the business, driving growth and profitability.
9. What challenges have you faced while trying to improve processes, and how did you overcome them?
Challenges include resistance to change, lack of resources, and aligning improvements with organizational goals. To overcome these, I communicate the benefits clearly, involve stakeholders early in the process, and provide necessary training and support. Demonstrating quick wins and maintaining open communication help build momentum and buy-in.
10. How do you ensure that process improvements are sustainable over the long term?
Sustainability is ensured by embedding improvements into the organizational culture, providing continuous training, and regularly reviewing processes. Establishing clear documentation and standard operating procedures (SOPs) and setting up monitoring mechanisms to track performance ensure that improvements are maintained and adjusted as needed.
11. In your experience, how does technology play a role in process improvement?
Technology plays a crucial role by automating repetitive tasks, providing real-time data for better decision-making, and enabling seamless communication and collaboration. Tools like TMS, ERP systems, and data analytics platforms enhance efficiency, accuracy, and scalability of process improvements.
12. How do you stay updated on best practices in process improvement?
I stay updated by attending industry conferences, participating in professional networks, and subscribing to relevant publications and journals. Continuous learning through online courses and certifications, and staying connected with industry experts and thought leaders, also help keep me informed of the latest trends and best practices.
13. Can you discuss a time when a proposed process improvement did not go as planned? What did you learn?
A proposed improvement to automate a portion of our supply chain faced technical issues and resistance from staff. The implementation was rushed without adequate testing and training. From this, I learned the importance of thorough planning, piloting new processes, and ensuring adequate support and training to facilitate smooth transitions.
14. How do you balance the need for process improvement with the potential for disrupting current operations?
Balancing the need involves careful planning and phased implementation. I conduct impact assessments to understand potential disruptions and develop mitigation strategies. Communicating clearly with the team, setting realistic timelines, and piloting changes in controlled environments help minimize operational disruptions.
15. What role does leadership play in supporting and driving process improvements?
Leadership plays a critical role by providing vision, resources, and support for process improvements. They set the tone for a culture of continuous improvement and encourage innovation. Their commitment and involvement are essential for overcoming resistance and ensuring successful implementation of changes.
16. How do you communicate process changes to a team resistant to change?
I communicate process changes by explaining the benefits clearly, addressing concerns, and involving the team in the planning stages. Providing training and support, highlighting quick wins, and maintaining open communication channels help alleviate resistance and build acceptance for the changes.
17. Can you explain the difference between process improvement and process re-engineering?
Process improvement focuses on incremental changes to enhance existing processes, aiming for efficiency and effectiveness. Process re-engineering, on the other hand, involves fundamentally redesigning processes from the ground up to achieve dramatic improvements in performance. Re-engineering is typically more radical and comprehensive than incremental improvement.
18. How do you handle feedback or resistance from employees during a process improvement initiative?
Handling feedback involves active listening, addressing concerns, and involving employees in the improvement process. Transparency, regular communication, and providing necessary support and training help mitigate resistance. Recognizing and valuing employee contributions foster a positive attitude towards change.
19. What metrics do you believe are most important when evaluating the effectiveness of a process improvement?
Key metrics include time savings, cost reductions, error rates, productivity levels, and customer satisfaction scores. These metrics provide a clear indication of the impact of the improvements and help identify areas for further enhancement.
20. How do you ensure compliance with industry standards when making process improvements?
Ensuring compliance involves understanding relevant industry standards and regulations, integrating them into the improvement plans, and conducting regular audits. Consulting with compliance experts and maintaining clear documentation help ensure that all process improvements adhere to required standards.
21. Can you describe a process improvement project that saved the company money or increased revenue?
I led a project to streamline our procurement process by implementing an automated purchasing system. This reduced manual errors, decreased processing time, and improved supplier negotiations. The initiative saved the company significant operational costs and improved inventory turnover, contributing to increased revenue.
22. How do you determine if a process can be automated or needs human intervention?
I determine this by analyzing the complexity and variability of the process. Routine, repetitive tasks with clear rules are ideal for automation. Processes requiring human judgment, creativity, or customer interaction are better suited for human intervention. Cost-benefit analysis and feasibility studies also guide the decision.
23. What is your experience with Lean, Six Sigma, or other process improvement methodologies?
I have extensive experience with Lean and Six Sigma methodologies, having led several projects utilizing these approaches. Lean focuses on eliminating waste and improving flow, while Six Sigma aims at reducing variability and improving quality. I hold certifications in both and apply these principles to drive continuous improvement.
24. How do you manage the documentation of process changes?
I manage documentation by creating detailed process maps, SOPs, and training materials. Using document management systems ensures that all changes are recorded, accessible, and easily updated. Regular reviews and audits help maintain accuracy and relevance of the documentation.
25. Can you give an example of how you've used data analysis in process improvement efforts?
In a warehouse management improvement project, I used data analysis to identify bottlenecks and inefficiencies. Analyzing picking and packing times, error rates, and inventory turnover helped pinpoint specific areas for improvement. Data-driven insights guided the implementation of changes, leading to a 20% increase in operational efficiency.
26. How do you ensure that process improvements align with the overall strategic goals of the organization?
Alignment is ensured by involving leadership in the planning stages, understanding the organization’s strategic objectives, and setting clear goals for the improvement initiatives. Regular reviews and communication with stakeholders help keep the improvements on track and aligned with broader organizational goals.
27. What is your approach to training employees on new processes?
My approach involves developing comprehensive training programs, including hands-on workshops, e-learning modules, and detailed training manuals. Providing continuous support, conducting regular refresher sessions, and creating a feedback loop for employees to ask questions and share concerns ensure effective adoption of new processes.
28. How do you deal with unexpected challenges that arise during the process improvement implementation?
Dealing with unexpected challenges involves staying flexible, maintaining open communication, and having contingency plans in place. Regular progress monitoring, quick problem-solving, and seeking input from the team help address and overcome challenges effectively.
29. Can you discuss the importance of customer feedback in process improvement?
Customer feedback is crucial as it provides direct insights into their experiences and expectations. Incorporating this feedback helps identify pain points and areas for improvement, leading to enhanced customer satisfaction and loyalty. Regularly seeking and analyzing customer feedback ensures that process improvements meet their needs and preferences.
30. How do you balance innovation with risk in process improvement projects?
Balancing innovation with risk involves thorough risk assessments, pilot testing new ideas, and setting clear parameters for acceptable risks. Encouraging a culture of innovation while maintaining a structured approach to risk management ensures that improvements are both creative and viable.
31. How do you ensure that process improvements are scalable as the company grows?
Ensuring scalability involves designing improvements with flexibility in mind, using technology that can scale, and standardizing processes where possible. Regularly reviewing and updating processes as the company grows helps maintain efficiency and effectiveness. Engaging in strategic planning ensures that improvements align with long-term growth objectives.
32. What is the most innovative process improvement solution you've implemented or proposed?
One of the most innovative solutions I implemented was using IoT sensors for real-time inventory tracking in our warehouse. This technology provided real-time data on inventory levels, reducing manual checks and errors. The integration of IoT with our inventory management system streamlined operations and significantly improved accuracy and efficiency.
33. How do you assess the return on investment for process improvement initiatives?
I assess ROI by comparing the costs of implementing the improvements with the benefits achieved, such as cost savings, time reductions, and revenue increases. Calculating metrics like payback period, net present value (NPV), and internal rate of return (IRR) provides a comprehensive view of the financial impact of the initiatives.
34. Can you explain how process improvement can lead to better employee engagement?
Process improvement can lead to better employee engagement by reducing inefficiencies and frustrations associated with outdated or cumbersome processes. Involving employees in the improvement process, providing training, and recognizing their contributions foster a sense of ownership and motivation. Streamlined processes also allow employees to focus on more meaningful and fulfilling tasks.
35. How do you prioritize stakeholder needs during a process improvement project?
I prioritize stakeholder needs by identifying key stakeholders, understanding their expectations and concerns, and involving them in the planning and implementation stages. Regular communication and feedback loops ensure that their needs are addressed and balanced with the overall goals of the project.
36. In what ways have you used technology to streamline or enhance business processes?
I have used technology to automate routine tasks, implement data analytics for better decision-making, and integrate systems for seamless information flow. Examples include implementing CRM systems to streamline customer interactions, using ERP systems for integrated resource planning, and leveraging cloud-based collaboration tools for improved teamwork.
37. How do you ensure that new processes are adopted and utilized properly across the organization?
Ensuring proper adoption involves comprehensive training, clear communication of the benefits, and providing continuous support. Setting up a feedback mechanism allows employees to report issues and suggest improvements. Regular monitoring and audits help ensure compliance and effectiveness of the new processes.
38. What is the biggest process improvement challenge you’ve faced, and how did you address it?
The biggest challenge was implementing a new ERP system across multiple departments. Resistance to change and technical issues were significant hurdles. Addressing it involved thorough planning, phased implementation, extensive training, and continuous support. Regular communication and involving key stakeholders early in the process helped manage resistance and ensure a smooth transition.
39. How do you incorporate sustainability considerations into process improvement?
Incorporating sustainability involves assessing the environmental impact of processes and identifying opportunities to reduce waste, energy consumption, and emissions. Implementing eco-friendly practices, such as using recyclable materials, optimizing resource use, and adopting renewable energy sources, helps ensure that process improvements align with sustainability goals.
40. Can you discuss a time when you had to improve a process with limited resources?
With limited resources, I improved our document management process by transitioning from paper-based to digital records using free or low-cost software. This reduced storage costs, improved accessibility, and increased efficiency. The project involved training staff on new tools and establishing clear digital documentation standards.
41. How do you manage the change curve in process improvement efforts?
Managing the change curve involves anticipating resistance, communicating effectively, and providing continuous support. I use change management models like ADKAR (Awareness, Desire, Knowledge, Ability, Reinforcement) to guide employees through the transition. Celebrating quick wins and providing ongoing training help smooth the change process.
42. What techniques do you use to identify process bottlenecks?
To identify bottlenecks, I use techniques such as process mapping, flowcharts, and value stream mapping. Analyzing performance data, conducting time studies, and seeking feedback from employees involved in the process also help pinpoint areas where delays or inefficiencies occur.
43. How do you convince leadership to invest in process improvement?
Convincing leadership involves presenting a clear business case that outlines the benefits, such as cost savings, efficiency gains, and improved customer satisfaction. Providing data-driven evidence, demonstrating alignment with strategic goals, and highlighting successful case studies from other organizations help secure leadership buy-in.
44. Can you share an example of cross-departmental process improvement you've been involved in?
I led a cross-departmental initiative to streamline the order-to-cash process, involving sales, finance, and logistics. By implementing an integrated ERP system and standardizing procedures, we reduced order processing time, minimized errors, and improved cash flow. Collaboration and regular communication among departments were key to the project's success.
45. What role does customer service play in your process improvement efforts?
Customer service plays a crucial role by providing insights into customer needs and pain points. Incorporating feedback from customer service teams helps identify areas for improvement that directly impact customer satisfaction. Ensuring that process improvements enhance the customer experience is a primary focus of my efforts.
46. How do you tailor process improvement strategies to different departments or functions?
Tailoring strategies involves understanding the unique needs and challenges of each department. I conduct specific assessments, involve department representatives, and customize solutions to fit their workflows and objectives. Flexibility and open communication ensure that improvements are relevant and effective for each function.
47. Can you discuss the role of collaboration in successful process improvement?
Collaboration is essential for successful process improvement as it ensures diverse perspectives and buy-in from all stakeholders. Involving cross-functional teams in planning and implementation, fostering open communication, and encouraging shared ownership of the outcomes lead to more effective and sustainable improvements.
48. How do you balance short-term fixes with long-term process improvements?
Balancing short-term fixes with long-term improvements involves addressing immediate pain points while planning for sustainable changes. Quick wins help build momentum and support, while strategic planning ensures that long-term goals are achieved. Continuous monitoring and iterative improvements help maintain this balance.
49. What's your approach to maintaining momentum and interest in continuous process improvement?
Maintaining momentum involves celebrating successes, recognizing contributions, and providing ongoing training and support. Regularly reviewing and updating processes, encouraging innovation, and fostering a culture of continuous improvement keep the organization engaged and motivated to pursue ongoing enhancements.
50. How do you evaluate the ethical implications of process improvements, especially in terms of data privacy and employee monitoring?
Evaluating ethical implications involves considering the impact on employee privacy, data security, and fairness. Ensuring compliance with data protection regulations, being transparent about monitoring practices, and involving employees in the decision-making process help address ethical concerns. Maintaining a balance between efficiency and ethical considerations is essential for responsible process improvement.